Monitoring and Innovation Strategies Working Group
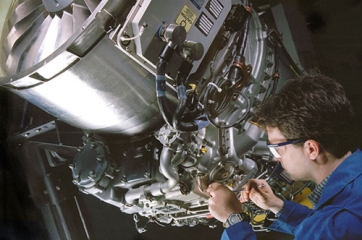
Workgroup members
- François Arrien, AV&R Aerospace
- Alain Aubertin, CRIAQ
- Francis Archambault, CTA
- Sylvain Boisvert, Safran Canada
- Yanik Boutin, Bombardier
- Louis Brunet, Collins Aerospace
- Mikael Cardinal, Unither Bioélectronique
- Patrick Champagne, CMC Électronique
- Cyrille Chanal, Fusia Groupe
- Phil Cole, Marinvent
- Jean Colpin, Université McGill
- David Pollack, Rolls-Royce Canada
- Sue Dabrowski, Libellule Monde
- Mathieu Demers, Avianor
- Michel Dion, Bell Textron Canada
- François Garnier, ÉTS
- Denis Lacroix, CTA
- Anne-Marie Lan Phan, Agence spatiale canadienne
- Sylvain Larochelle, Pratt & Whitney Canada
- Éric Laurendeau, École Polytechnique de Montréal
- Louis-Philippe Lemaire, Créaform Ingénierie
- Jonathan Lévesque, INO
- Mouhab Meshreki, CNRC
- Christian Moreau, Université Concordia
- Peter Rosenthal, CNRC-PARI
- Dominique Sauvé, SA2GE
- Marc-André Talbot, Thales Canada
Canadian industry is increasingly facing competition from emerging countries such as China and India, two countries that are investing heavily in their manufacturing sectors. In order to remain a leader, Québec’s aerospace industry needs to boost its innovation efforts.
The working group’s mandate is to define an aerospace innovation strategy and action plan for Québec and to establish and coordinate projects that support this strategy. It covers everything from concept to commercialization, from private research to public and academic research, in close collaboration with the Consortium for Research and Innovation in Aerospace in Québec (CRIAQ) and the Consortium for Aerospace Research and Innovation in Canada (CARIC). (Created in 2006)
Objectives
- To establish an initiative aimed at developing a strategy for aerospace innovation in Québec.
- To identify and coordinate initiatives for structuring projects in support of the innovation strategy.
- To work with other innovation organizations to ensure good coordination and avoid duplication of efforts.
Key projects:
- SA2GE – Greener Aircraft Mobilizing Project
- Aéro21 strategic mobilizing project
- Aerospace Innovation Forum
Working Group Committees
- Ideas Committee (innovation)
- Aéro 21 Committee
- SA2GE Committee (external link)
- Recycling Committee (SA2GE)
- SME and Innovation Committee
- AI and Disruptive Technologies Committee
Workgroup President
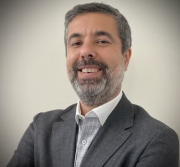
Houssam Alaouie
Workin Group President,
Global Head of Collaboration
and Government Programs,
and Academic Partnerships
CAE